Tyromer’s Tire Devulcanization Systems are Highly Recognized by TRIB
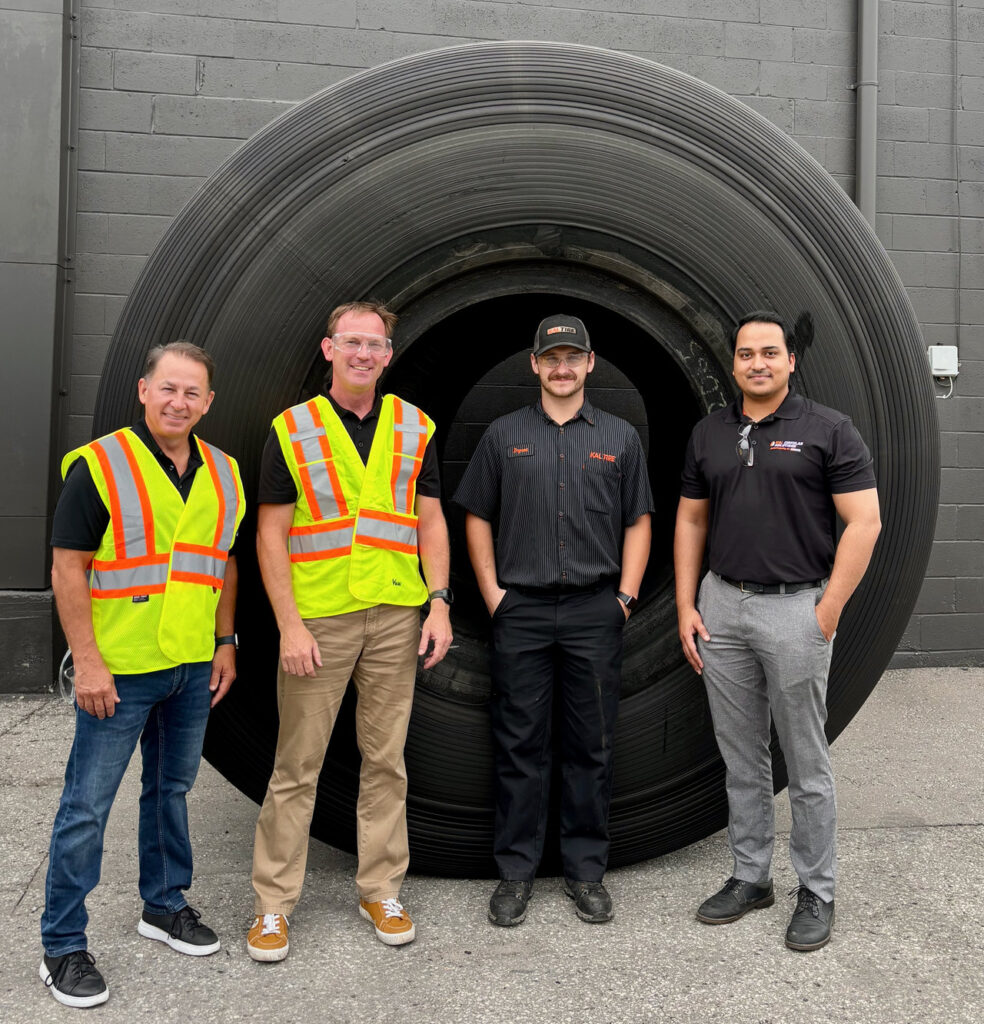
Tyromer Devulcanization Systems are Highly Recognized by TRIB Recently, a delegation from the Tire Retread & Repair Information Bureau (TRIB) visited the Ontario-based Oshawa facility of Kal Tire, a leading Canadian tire manufacturer, to gain in-depth insights into its advanced desulfurization system. Kal Tire has long been committed to developing high-quality tire products. With rising global environmental awareness, tire recycling has become a critical industry focus. To align with sustainability goals, Kal Tire adopted an innovative Tyromer desulfurization system, which processes waste tire rubber into tire-derived polymer (TDP), enabling tire reuse and reducing environmental pollution. Below is a translated excerpt from TRIB’s official website article about the visit: I recently had the chance to visit Kal Tire’s OTR Tire Retread & Repair facility and their devulcanization facility in Oshawa, Ontario. I was met there by Darryl Moore, Director, Business Development Remanufacturing and Sustainability Solutions, Jon Corey, Retread Facility Manager, and Paresh Kulkarni, Devulcanization Facility Manager. In addition to Kal Tire’s Bandag commercial truck retread facilities throughout Canada, Kal Tire also has two OTR retread and repair facilities in Canada; the one in Oshawa that I visited and one in western Canada in Kamloops, British Columbia, in addition to 4 other OTR repair facilities. The thirty team members at the Oshawa retread facility work two shifts to produce more than 2,000 OTR retreads per year and process a roughly equivalent number of repair-only tires. We walked through the retread process from start to finish and of course, began at the critical initial inspection phase. The experienced team members who work in this section carefully inspect every tire that comes into the facility to determine whether it can be repaired or retreaded. Depending on the size of the tires and the locations the tires are coming from, it can take up to three days to inspect 40 to 50 tires. A mistake at this stage of the process can lead to hours of lost productivity for the facility, especially if a tire starts going through the retread process and is later determined not to be a good candidate for retreading. It’s an important point to stress about retreading… only carefully inspected tires that pass quality control measures go into the retreading process. Quality in equals quality out. At this stage, Kal Tire also removes any previous patches installed so they can re-install the patches and ensure they meet Kal Tire’s specifications for repairs. From here, we move on to the buffing and regrooving stations where the expired tread is first peeled off in larger pieces and then the tire carcass is buffed to the appropriate texture for retreading. Again, depending on the size of the tire, the buffing process can take an average of 30 minutes, while regrooving tires can take up to 90 minutes. As we’ll see later, Kal Tire is very focused on sustainability, and they use a closed-loop tower collection system that captures all the peeled rubber and buffings to be recycled. Next, it’s on to skiving which can also be a productivity challenge given the amount of manual labor required to skive out damage to the tires to prepare them for repair. Three full-time team members work each shift and skive between 1 and 6 tires per day. This is just one other indicator of the amount of skilled labor that goes into each of these tires during the retread process. As we move on to the repair section, the well-trained and experienced team members carefully make repairs, install new patches, and fill skives in final preparation for the repairs either being cured and the tires returned to service or getting prepped to be built and put into molds/chambers for retreading. It’s important to note here that Kal Tire uses 25% reclaimed rubber in their compound formulations for their use in OTR retreading. This reclaimed rubber comes directly from the capture of buffings and other used rubber from Kal Tire’s retread facilities. Finally, the tires move on to the curing phase of the retread process. The curing chambers in Oshawa can handle tires up to 57 inches in diameter and can take up to six hours to cure. Now we move across the street from the retread plant to the devulcanization facility and on from rebuilding tires to reusing rubber buffings in the production of tread rubber. Becoming operational in January 2024, the devulcanization line is the most advanced fully-operable devulcanization facility in North America. Kal Tire’s partnership with Tyromer (who owns the Intellectual Property for the devulcanization process) has allowed them to recycle their retread buffings back into the tread rubber for their OTR retreads. Commercial truck tire buffings are collected from Kal Tire’s various Bandag retread facilities and delivered to the devulcanization facility in Oshawa. Non-contaminated rubber is critical to the devulcanization process and the buffings go through several cleaning and separation steps before moving on to devulcanization. First, the rubber buffings are fed through a magnetic drum that pulls out any metal contaminants and grinds the rubber from 4 to 10 mesh down to 14 to 30 mesh. The buffings are then run through a gravity separator and re-fed through the grinder as needed to get to the perfect mesh size. After this, the buffings are run through a de-stoning machine that separates any tiny rocks or gravel that have survived the grinding process. The buffings are then collected in 2,000-pound bags and transferred to the devulcanization and extruder equipment located in a separate building. Using carbon dioxide, heat, and pressure, the rubber is devulcanized and the various component outputs are collected, including the now-devulcanized rubber which is extruded, passed through a second rock cleaning process, water-cooled, run through a dryer drum, applied with protective film, and cut to the correct length. As a final quality check, the material is run through a metal detector one last time to detect any stray contaminants before being shipped to their rubber compounder, Air Boss. This devulcanized rubber then goes into the tread rubber manufacturing process for materials that Air Boss will ship
Material Handling Conveyors Go Green CN
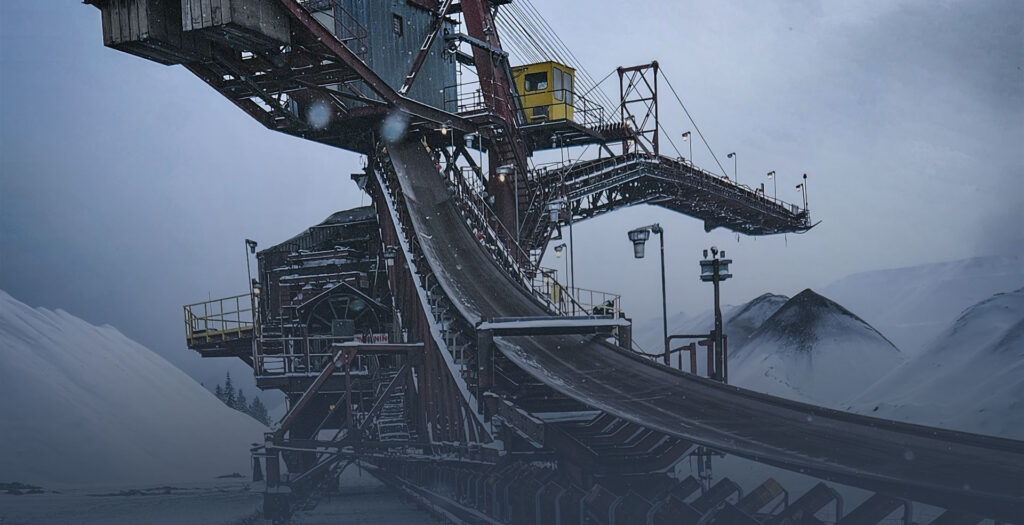
Material Handling Conveyors Go Green Waste mining tires are transformed into a new material for use in conveyor manufacturing. Giant mining tires and conveyor belts are made of high-performance rubber and, due to perceptions that recycled rubber cannot effectively replace virgin rubber in tangible amounts, these materials have, historically, presented a sustainability challenge within the tire and rubber industry. Waste off-the-road mining tires (wOTR) pose significant sustainability challenges due to the high costs and logistical complexities that come with them. In some cases, only 6 tires can be shipped on a single transport truck. These are highly engineered products, comprised of natural and synthetic rubber compounds, numerous reinforced protection ply layers, and steel belts. A single haul truck tire can weigh up to 5 metric tonnes (11,000 pounds), stand 15 feet tall, and contain enough steel to make a small car. However, tough as they are, like all tires, these tires wear out, and in Canada alone, thousands of them need to be replaced annually. With no national or international mining tire recycling programs or commercially viable recycling opportunities currently available, worn-out tires represent one of the largest sources of industrial waste generated by mining operations. While some companies are actively repurposing retired OTR tires for temporary uses like building retaining walls or civil engineering projects, around 80% of companies either stockpile or dispose of these tires in landfills. This has created an enduring challenge, OTR tires do not biodegrade due to their chemically inert constituent materials. Whether they are left on-site or placed in landfills, OTR tires are not going anywhere. The Teck team undertook a lot of research. They looked at vendors capable of downsizing a 5-ton, 15 ft high giant mining tire. They studied the technologies available to reclaim or regenerate the rubber. Technologies — devulcanization, waterjet, thermal conversion (pyrolysis), micronization, as well as other tier 2 and tier 3 options to recycle giant mining tires. These were researched and then ranked in terms of which options were the most environmentally friendly — zero waste and discharge, energy used to recycle, GHG friendly. Ultimately devulcanization and waterjet technologies were two the team chose to pursue. It was important to find the most environmentally friendly and sustainable way to transport the tires. This was accomplished by implementing backhauls or trucks that were going back empty and by using rail to transport materials. This accomplished, the team also set out to upcycle the rubber crumb so that it was not merely being used as landscape mulch or for making rubber mats. Their objective was to displace virgin rubber being imported and ultimately this rubber crumb was reclaimed using devulcanization and partially replaced virgin materials. The goal was to develop a technology that would reclaim the waste into a quality rubber which end users would buy, compound and permanently adopt and, using the Tyromer technology to develop tire-derived polymer (TDP), and remarkably, they did just that. Collaborating with strategic partners, Teck worked with Liberty Tire to mechanically separate OTR tires, recycle steel components, and provide the residual crumb rubber. Teck then upcycled this rubber crumb using Tyromer’s devulcanization technology to bring the spent crumb rubber back to life. Fenner Dunlop then integrated the team’s TDP into new conveyor belts, after compounding and rigorous testing phases. These belts were put to work and monitored at one of Teck’s mining operations in BC, but getting to that stage was no mean feat. Convincing both management and maintenance personnel required persistence and technical guarantees from the manufacturer because a lot is riding on these tires. After all, a premature failure causing downtime at Canada’s largest open-pit copper mine would be costly, and impact adoption and any future pilots. After the initial pilot, the initiative expanded with belts being tested at multiple Teck sites and, depending on the application, monitored for abrasion resistance and performance. The success of these initial efforts provided confidence to develop a new fire-retardant compound to expand the product line. This required CSA certifications from a third party, and the end result, after stringent testing, was the manufacture of a 3,368 ft conveyor belt weighing 63,318 lbs, installed at one of Teck’s mining operations. The success of their CSA-C fire-retardant belt has encouraged a third-party mining company to purchase and install a conveyor belt at one of their operations in Canada. Teck’s innovative but careful approach to the task they set themselves is what enabled them to work collaboratively with industry giants like Michelin, Fenner Dunlop and Continental, shifting perceptions within the conservative tire and rubber sector. Proving that regenerated rubber can indeed replace virgin rubber in substantial quantities is a game changer, reducing the environmental footprint of mining operations and promoting circular economy principles in industrial manufacturing. 54 inch wide x 3,368 ft fire resistant conveyor belt installed In addition to achieving sustainability objectives and contributing to the circular economy, Teck’s innovative pilot projects have set new industry standards and proven the concept of transforming waste into valuable resources. These efforts help prevent deforestation associated with rubber cultivation by providing a sustainable domestic alternative to imported rubber, contributing significantly to Canada’s manufacturing sector’s reduced reliance on foreign materials. Sometimes “What goes around comes around” is a dire warning, but coming from Teck Resources Limited, it’s a very hopeful start. Article according to: CLEAN 50
Tyromer Selected for the AWS Clean Energy Accelerator 4.0
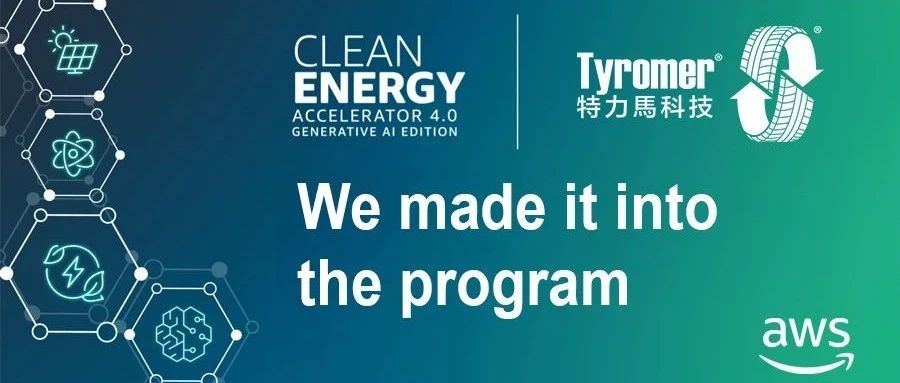
Tyromer Selected for the AWS Clean Energy Accelerator 4.0 Amazon Worldwide Operations Sustainability. The enterprise acceleration program is set to support decarbonization at scale through client venturing August 14, 2024 — Amazon announced today that Tyromer has been selected as one of the 21 startups out of over 800 candidates from 74 countries that will participate in the Amazon Web Services (AWS) Clean Energy Accelerator 4.0 I Generative AI edition in the circular economy focus area, a high-pace, non-equity dilutive accelerator designed to support enterprise customers decarbonize at scale, through co-innovation with emerging clean energy and climate tech solutions by mature startups. The program is focused on helping accelerate net zero pathways and the deployment of circular economy solutions to meet the world’s growing energy needs and to preserve depleting resources. “We’re pleased to welcome Tyromer into the Clean Energy Accelerator 4.0 as we work together to accelerate energy transitions through generative AI and grid modernization,” said Howard Gefen, General Manager of Energy and Utilities, AWS. “With focus areas spanning from sustainability to clean energy, to alternative fuels, we’re excited for this collaboration in helping us reach our net zero goal.” “We are excited to join the AWS Clean Energy Accelerator and work towards overcoming clean energy and decarbonization challenges,” said Jon Visaisouk, COO. “Through this program we can help define and shape the future of clean energy, climate tech and circular economy innovations.” The circular economy is one of the focus areas of the AWS Clean Energy Accelerator 4.0. Amazon Operations Sustainability has joined the program as a piloting partner, looking for breakthrough solutions in low carbon building solutions, circular economy, sustainable fleet and mobility, and low carbon fuel technologies. Tyromer is excited to collaborate with Amazon Operations Sustainability to pilot tires containing TDP (Tire-Derived Polymer), a devulcanized tire rubber made from end-of-life tires, to introduce the Tyromer Tire-to-Tire vision for sustainable mobility. The AWS Clean Energy Accelerator 4.0, which was announced at COP28 and kicked off in March 2024, has selected its cohorts. Throughout the year it will bring the participants and piloting partners into immersion sprints and workshops to dive deep into piloting opportunities in addition to events to showcase clean energy technology innovations, pilot progress and new use case developments to an audience of leaders in the energy space, industry experts, private and public sector and investors. Learn more about the AWS Clean Energy Accelerator at: www.aws.amazon.com/energy/clean-energy-accelerator
Tyromer recognized by U.S. Government, Selected for Grant Programs
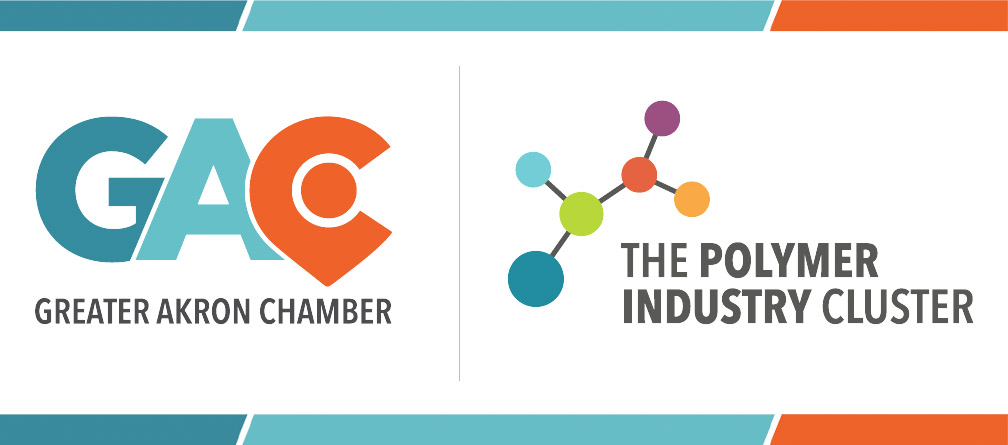
Greater Akron Sustainable Polymers Tech Hub Proposes Broad Action to Anchor the Future of Sustainable Polymers Technology Akron, OH – Earlier today, partners of the Polymer Industry Cluster, housed at the Greater Akron Chamber and recent designee as the federal Sustainable Polymers Tech Hub, submitted a proposal to receive funding from U.S. Department of Commerce Economic Development Administration’s (EDA) Regional Technology and Innovation Hubs Program (Tech Hubs). In this application, the Polymer Industry Cluster proposes to use EDA funds to implement eight Sustainable Polymers Tech Hub projects that collectively: Enhance a sustainable governance model with focus on partnership growth, Open Innovation, Evaluation, and Risk Mitigation; Reinvigorate the polymer startup ecosystem and increase investment resources for innovators; Add new workforce capacity in Sustainability and Life Cycle Assessment; and Invest in technology that enhances polymer performance, while reducing environmental impacts. The proposal requests a total of $70 million for this work, matched by over $11 million in public and private investment. The projects will be implemented over a five-year period, with the goal to create or retain over 6,300 jobs; catalyze $1.8 billion in direct private investment; and achieve an annual CO2 reduction of 3.9 million tons (equivalent to taking nearly 1 million cars off the road). Synthetic polymers, such as rubber, plastics, and adhesives, are strategic materials that have helped address some of society’s most important challenges. However, conventional polymers, derived from fossil fuels, produce greenhouse gas emissions, pollution, and non-biodegradable scrap that have major environmental consequences. The award announcements are expected in the summer of 2024, with funded projects expected to begin in October. In the interim, the Polymer Industry Cluster will continue its work convening strategy groups focused on consortium governance, communications, and impact evaluation, and strengthening the fabric of collaboration for the benefit of research, innovation and investment in the industry. While the submission of this proposal is one more step in the work of the Polymer Industry Cluster to double down on our region’s roots in the polymer industry and leverage our industry assets to create jobs, investment, innovation and opportunity. About the Proposal The vision of this proposal centers around the goal of accelerating the commercialization of sustainable polymers while equitably benefiting the people and businesses of Greater Akron. Drawn from a larger pipeline of technology maturation projects, this proposal brings forward five projects with groundbreaking technological potential and further invests in governance, workforce, and startup-focused assets to accelerate impact beyond Tech Hubs. The result is an initiative that directly integrates exciting polymer innovations into the value chains of global corporate end-users with line of sight to worldwide deployment. Each of the eight projects are being led by a Polymer Industry Cluster partner, each making a direct funding request to EDA under the Sustainable Polymers Tech Hub umbrella. Partners leading component projects include Bioverde Tech LLC, Bounce Innovation Hub, Flexsys, Full Circle Technologies / Tyromer (co-leads), Huntsman Corporation, The Goodyear Tire & Rubber Company, The Greater Akron Chamber, and The University of Akron. The eight projects were selected after rigorous exploration and deliberation of the partners and stakeholders of the Polymer Industry Cluster. Support and engagement for this application was garnered from an unprecedented 77 public and private partners, including corporations, institutions of higher ed, government, economic and workforce development, labor, and community organizations. Through this work, the Sustainable Polymers Tech Hub aims to enhance Greater Akron’s global competitiveness and increase climate and environmental sustainability in the manufacturing of rubber and plastics locally and across the globe. The proposal is born from a rich history and density of polymer companies in Akron, Ohio, making it a ripe opportunity for the region and the country. Anchoring a region with 1,200 companies and 42,000 workers in the polymer sector, Greater Akron has the largest concentration of polymer plants, machines, and materials in North America. Renowned for its technical expertise and innovation, our region is positioned to be America’s best location to catalyze sustainable polymer technology for global impact. The submission of this proposal and the preceding designation as the Sustainable Polymers Tech Hub, create unparalleled opportunities for Greater Akron and Northeast Ohio, as a whole. The opportunity to apply for investment opportunities like this one will catalyze new industry, support the growth of innovation, increase the growth and attraction of businesses in this industry, and drive economic growth in our region across all sectors. Beyond this, an intentional focus on inclusive economic growth is illustrated in this proposal, thus reinforcing the commitment to ensuring all of Greater Akron’s residents experience the opportunities that can be created during this next phase of our region’s history. We are greatly encouraged by the broad bipartisan support this proposal has received from Ohio’s Congressional Delegation, the DeWine Administration, Ohio Legislature, and local government leaders. The partnership and backing of our elected officials helped us get to where we are, and we look forward to continuing to work with them on securing what will be a transformational investment for one of Ohio’s most critically important industries. We have also received wide support from a broad network of economic development partners and organizations in Northeast Ohio and beyond including significant investment committed from JobsOhio to match more than $4 million committed by a broad range of private sector companies, philanthropic organizations, Summit County and the City of Akron. About the Greater Akron Chamber The Greater Akron Chamber is a business membership and economic development organization serving Summit, Medina, and Portage counties. The Greater Akron Chamber drives economic growth and prosperity for the region by supporting the success of the business community and acting as a convener of stakeholders on key issues facing Greater Akron. About the Polymer Industry Cluster The Polymer Industry Cluster Initiative was launched in 2021 to conduct a deeper examination of the region’s polymer industry and develop a framework to leverage its full potential. Powered by the Greater Akron Chamber, the Polymer Industry Cluster works to elevate Northeast Ohio’s polymer industry into a truly dynamic enterprise that is better positioned
Apollo Tyres and Tyromer Announces Partnership
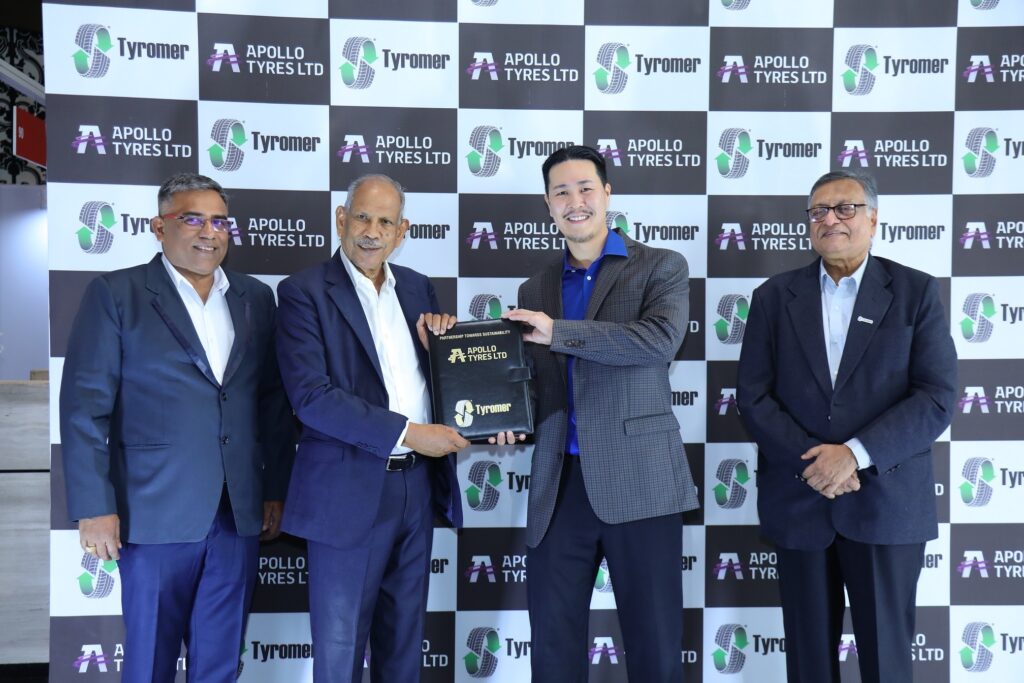
Apollo Tyres and Tyromer Announces Partnership Tyromer Inc, through its Indian associate, Tyromer India LLP, is committed to supplying recycled rubber material, produced using its environmentally sustainable processes, to Apollo Tyres. Home-grown tyre manufacturer Apollo Tyres has partnered with Tyromer Inc, a leader in the non-chemical devulcanization of end-of-life tyres. Tyromer Inc, through its Indian associate, Tyromer India LLP, is committed to supplying recycled rubber material, produced using its environmentally sustainable processes, to Apollo Tyres. P K Mohamed, Chief Advisor, R$D, Apollo Tyres Ltd, said “This partnership with Tyromer is a step towards achieving our sustainability goals, and it also enables us to honour our Extended Producer Responsibility (EPR). Producing new tyres using sustainable raw materials, is currently the most efficient path to meet our circular economy goals.” Commenting on the partnership, Dr Sam Visaisouk, CEO, Tyromer Inc, said “We are thankful to the Apollo Tyres’ team for its support of our vision of direct tyre-to-tyre recycling for achieving a tyre circular economy. In the face of climate crisis, not using rubber derived from end-of-life tyres is no longer an option.” This partnership has validated tyre-derived polymer (TDP), produced by Tyromer’s proprietary and patented technology, as the raw material for tyres. Tyre-derived polymer (TDP) trivia: Using a tonne of TDP saves GHG emissions equivalent to 4 passenger vehicles driven for a year Producing a tonne of TDP requires less than 2 MWh of energy, compared to over 20 MWh required for new material
Tire to Tire recycling: Partnership between Tyromer and Continental Tires
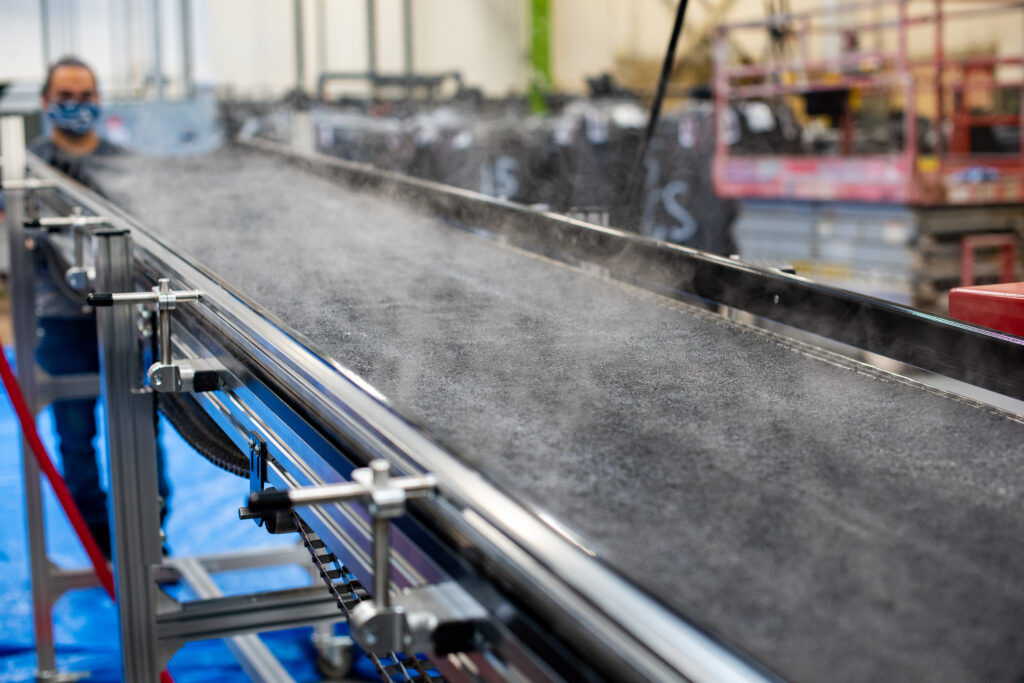
Tire to Tire recycling: Partnership between Tyromer and Continental Tires WATERLOO, CANADA AND ARNHEM, THE NETHERLANDS (November 14, 2022). Tyromer is pleased to announce that its recycled rubber material, produced via its environmentally sustainable, non-chemical extruder devulcanization of end-of-life tire rubber, is now used by Continental Tires. This is the result of a multi-year collaboration driven by the shared commitment of the two companies to circular economy in which end-of-life tire rubber is reused in the production of new tires. Tire-to-Tire recycling represents in many cases the most direct and energy efficient way to reuse what is still largely considered and treated as a waste. Tire rubber compound accounts for over 80% of the CO2 emission from raw material production for a tire. Using TDP to replace virgin rubber compound will provide more than 90% CO2 emission reduction. As we move towards renewable energy and electric mobility, tire rubber compound production will be responsible for more than 50% of the lifecycle CO2 emission of a tire. Reducing CO2 emission from raw material production has never been more urgent. “Tyromer is a trusted partner of ours supplying recycled rubber material. At Continental, we focus since many years on technologies that generate high-quality feedstock derived from end-of-life tires to produce new tires. Our goal is to gradually use 100 percent sustainably produced materials in our tire products by 2050 at the latest.” says Dr. Andreas Topp, Head of Materials and Process Development and Industrialization at Continental Tires. “We could never have done it alone. Our collaboration with Continental Tires has taught us lessons in quality, reliability, consistency, among many others. We are grateful for the support and the guidance to tailor the specifications of our recycled rubber material according to Continental’s specific needs.” says Dr. Sam Visaisouk, CEO of Tyromer. “All of us at Tyromer are proud to be part of the solution.” About Tyromer. Tyromer Inc. is a Canadian company founded in 2009 in Waterloo, Ontario, Canada. Using an open innovation business model to collaborate with tire industry leaders, Tyromer licenses its TDP production technology and systems around the world in order to establish a distributed supply chain so tire producers can “buy local.” Tyromer welcomes partners to advance its Tire-to-Tire vision for a circular economy. Click here to view Conti Supplier Rating 2023.pdf
Tyromer chosen as Top 100 private companies in North American by Red Herring
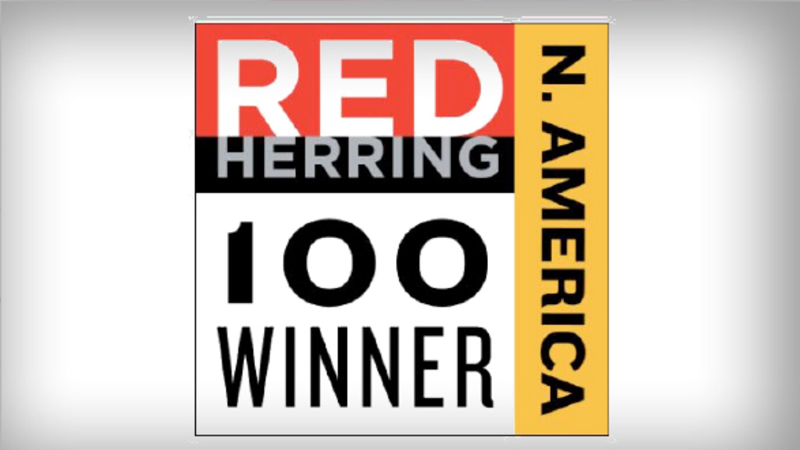
Tyromer chosen as Top 100 private companies in North American by Red Herring On June 14, 2017, Tyromer Inc. was named a winner of the 2017 Red Herring Top 100 North America event in Los Angeles, California, being recognized as one of the continent’s most exciting and innovative private technology companies. Sam Visaisouk, CEO, Tyromer Inc. thanks Red Herring and its judges for selecting the company a Top 100. Among the selection criteria were: social contribution, disruptiveness of the solution in its respective markets, market size, market maturity, growth rate, branding, CEO/Team quality, experience and track record. Globally over one billion scrap tires are generated this year, and more next year. Not much scrap tire rubber is reused in tire manufacturing even though the tire industry consumes more than 50% of the global rubber supply. Tyromer provides a socially responsible and environmentally sustainable solution to the global scrap tire problem using its patented supercritical carbon dioxide extrusion technology to devulcanize scrap tire rubber to produce TDP (Tire-Derived Polymer) for reuse in tire manufacturing. It is now possible to implement a circular economy in the tire industry.
Tyromer honored with prestigious 2018 James L. White Award
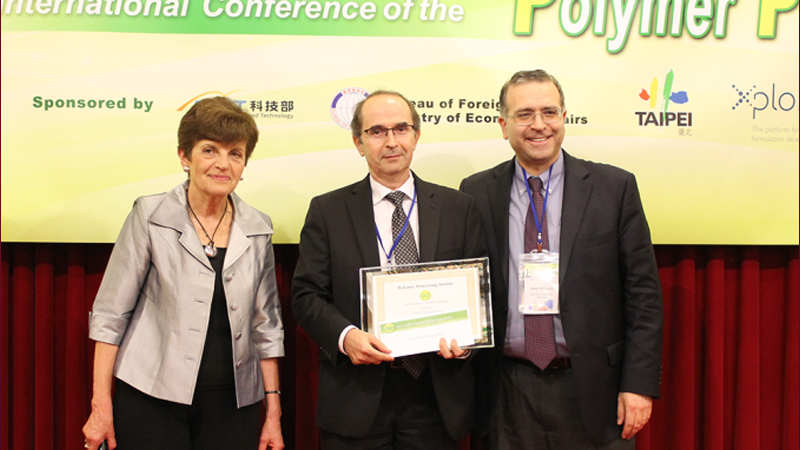
Tyromer honored with prestigious 2018 James L. White Award Tyromer Inc. congratulates Professor Costas Tzoganakis, the inventor of its patented supercritical carbon dioxide assisted twin-screw extrusion technology for rubber devulcanization, for receiving the prestigious 2018 James L. White Award: Prof. Costas Tzoganakis is the recipient of the 2018 James L. White Award from the Polymer Processing Society. The award is for an innovative development in the field of polymer processing technologies with recent commercial impact. It aims to recognize originality, innovation and creativity among researcher(s) or inventor(s) in the science and technology of processing polymers and polymeric products. Prof. Tzoganakis received the award during the 34th International Conference of the Polymer Processing Society in Taipei May 21-25, 2018 in recognition of his Tyromer ® rubber devulcanization work.With Professor Tzoganakis’ invention, waste tire rubber can be reused in tire manufacturing to enable a circular economy that is socially responsible, environmental sustainable and financially viable.
China Expanding Blue Skies Initiative to Curb Pollution
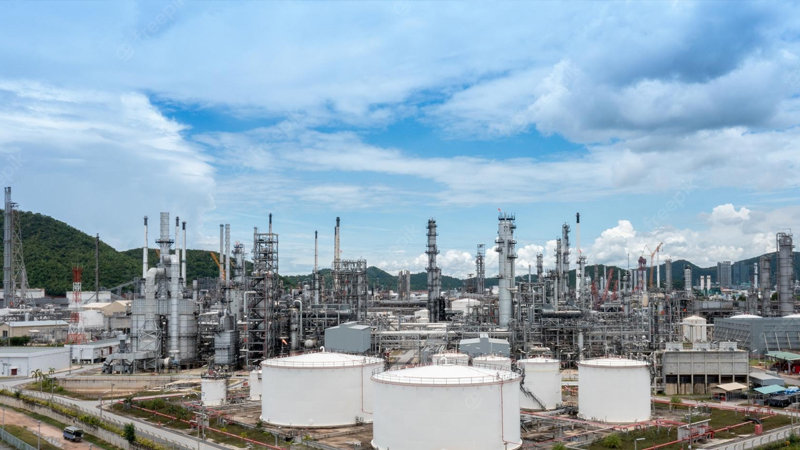
China Expanding Blue Skies Initiative to Curb Pollution China has announced plans to extend its cutbacks on air pollution in advance of the Winter Olympics being held in Beijing this year. The move is one that could have heavy impacts on the coal and steel industries, as the air particulate requirements would extend from the Beijing and Tianjin municipalities and include 62 cities in northern and central provinces. Among those areas are the cities of Tangshan and Handan, hubs of key steel production, and Shanxi, Shaanxi, and Henan, all of which are major coal-producing provinces. Clean energy companies in China are continuing to experience exponential growth since the original announcement this time last year by President Xi of the 2060 goals. LONGi Green Energy Technology Co, the global leader in manufacturing of solar modules is up around 50% in the last year, and the top wind turbine maker in China, Xinjiang Goldwind Science & Technology Co., is up over 80% over last year.
Tyromer Wins 2018 BIG Sustainability Leadership Award
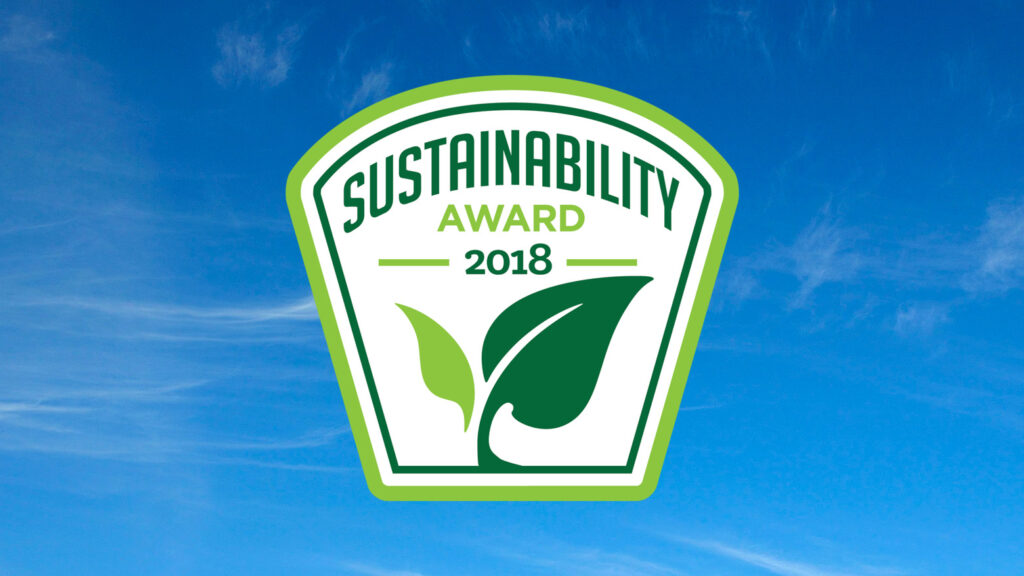
Tyromer Wins 2018 BIG Sustainability Leadership Award PHILADELPHIA, July 17, 2018 – Tyromer Inc. has won a 2018 Sustainability Leadership Award from Business Intelligence Group (BIG). Headquartered in New Jersey, USA, BIG Awards seek to recognize companies and individuals with persistence, vision, and creativity. “We are proud to recognize Tyromer Inc. for their socially responsible and environmentally sustainable effort on waste tire recycling,” said Maria Jimenez, Chief Nominations Officer, Business Intelligence Group. “Our judges felt that their vision and strategy make a significant impact in driving the circular economy in the tire industry, and gave Tyromer the highest rating as reflected by the Sustainability Leadership Award. Congratulations!” The BIG Award for Sustainability Leadership continues the company’s upwards trajectory. Earlier this year Tyromer won an Edison Award Gold Medal, considered the “Oscars of Innovation,” in the category of Resource Re-use. Additionally, the Company was named one of the Top 50 Fastest Growing Companies by Silicon Review Magazine. Despite Tyromer’s global outlook, CEO Sam Visaisouk hasn’t forgotten its Ontario roots. “Our success thus far would not have been possible without the University of Waterloo, Ontario Centres of Excellence and Michelin Development, all of whom gave us the early support for our vision to return waste tire rubber to new tires,” he says, adding, “Sustainability happens when we care.” The company uses the non-chemical solvent rubber devulcanization technology for which Professor Costas Tzoganakis was named the winner of the prestigious 2018 James. L. White Innovation Award by the Polymer Processing Society. The Tyromer Waterloo, Ontario plant is the first non-chemical commercial scrap tire rubber devulcanization operation in the world. It represents the “Best Practice” in scrap tire management where scrap tire rubber is reused for its original intended purpose. Currently, most scrap tires are burned for their fuel value, some are ground into crumb rubber and downcycled into fill for playgrounds and rubber mats, for example. Tyromer will change that, with its upcoming plant in Windsor, Ontario, to provide devulcanized scrap tire rubber for new passenger and truck tires, and numerous licensed plants under development around the world.